
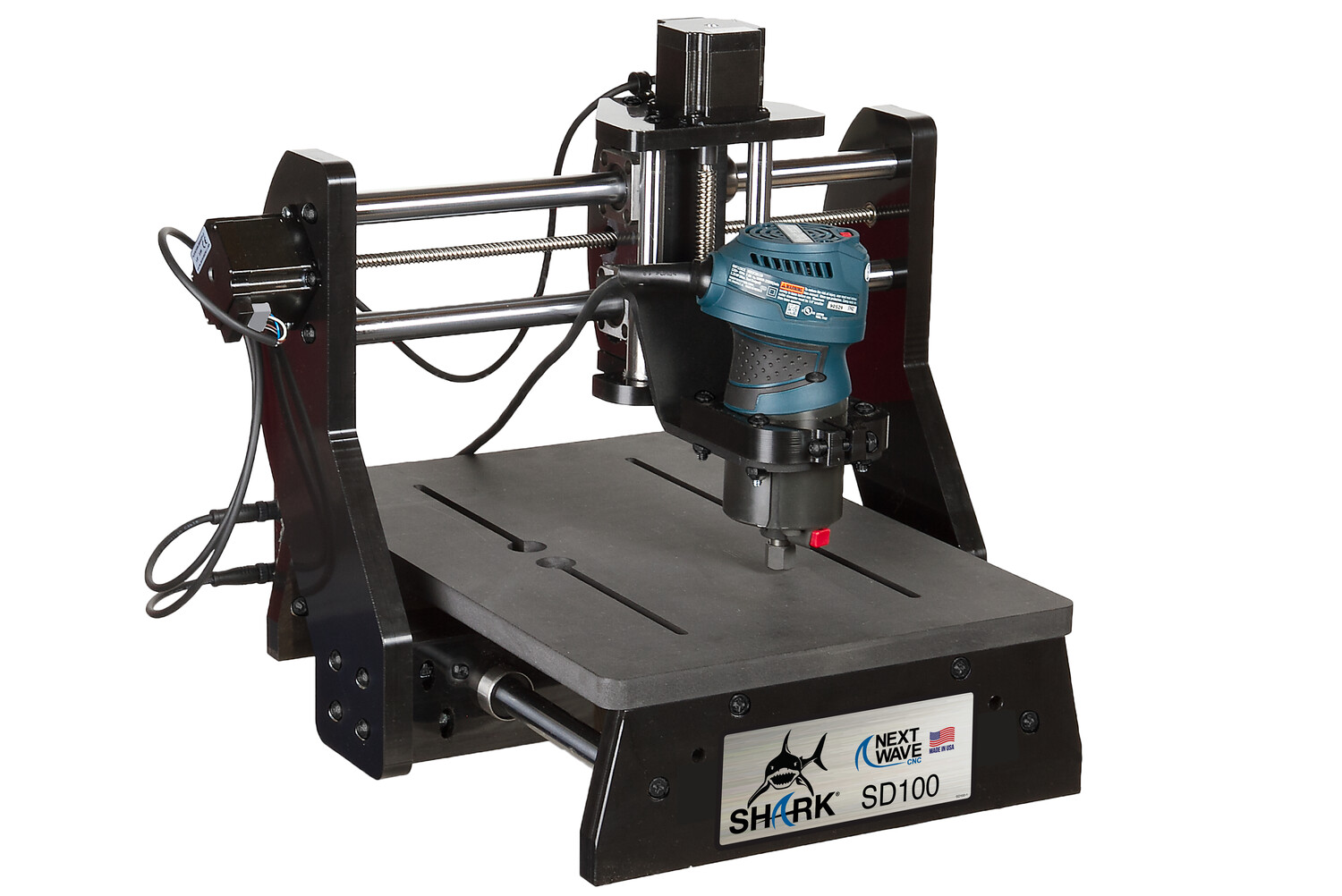
On that plate, I milled a portion down 0.010". I use a script to automatically zero the tool by touching a 0.500" plate. The photo shows how I lie to the software upon occasion when cutting a non-uniform thick piece of plywood. Two, place the touch plate near a hold down clamp when indexing from the top of your material to avoid measuring on a warped area of the stock, and three, lie to the software by indexing a little lower than your touch plate thickness. One, tell the software that your material is the thickest that you have measured. I generally index from the top of my material so in order to compensate for variations in thickness to insure that my profile cut-outs cut through the material, I employ a couple of different strategies. If I measure stock plywood, it can vary by 0.006 or more. If I run stock through a thickness sander and measure with a caliper, I find the thickness varies by about 0.003" or so. Once that's determined, it's important that the touch plate is located to give the best average (or in some cases, greatest) thickness. Like the others have said, it depends on the job. This will help you decide which makes more sense overall for a particular project. Just think through the project, think about whether the material thickness varies (and if it matters), and what your final goal is. There are other reasons for Zeroing from Top or Bottom. Effectively, this means you are Zeroing from the same side of the material when swapping between Top/Bottom Zero locations. For example, Zero from the Top for the first side, then Zero from the Bottom after flipping the material to machine the opposite side. Zeroing from the bottom assures the bit will protrude from the bottom as specified in your layout.ģ) For two-sided projects you may want (or need) to change your Zero to the opposite when flipping over material. Plywood material particularly can have thickness variations on the same sheet. This assures the depth of the cutter from the top surface of the material is consistent.Ģ) Zero from the bottom if consistent cut-throughs for "plain panel parts" and the like is desired.
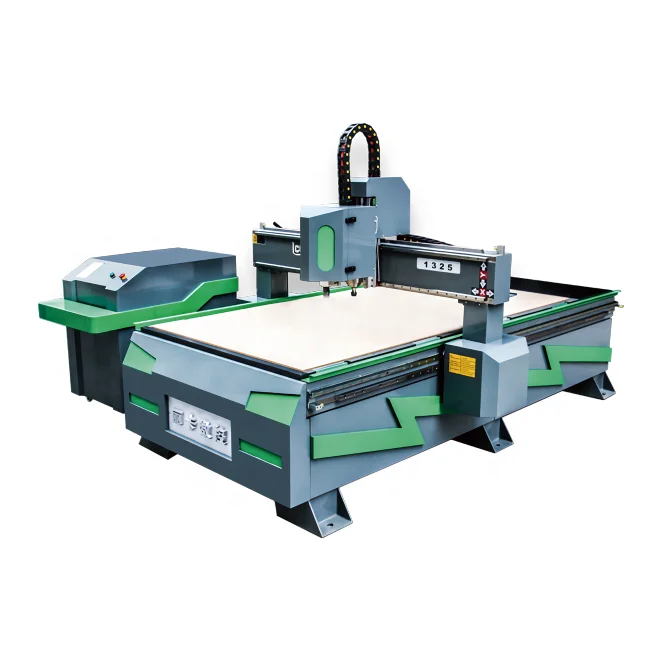
Possible reasons to alternate.ġ) Zero from the Top when doing v-carving or dados/slots. Different jobs may make more sense for one or the other. There are several reasons to Zero from the Top and/or to Zero from the Bottom. Will compensate for this and be Z zero directly on the top of the material? My touch plate is approximately 1/8" thick. Setting the Z zero on the top of the material seems to make more sense.
